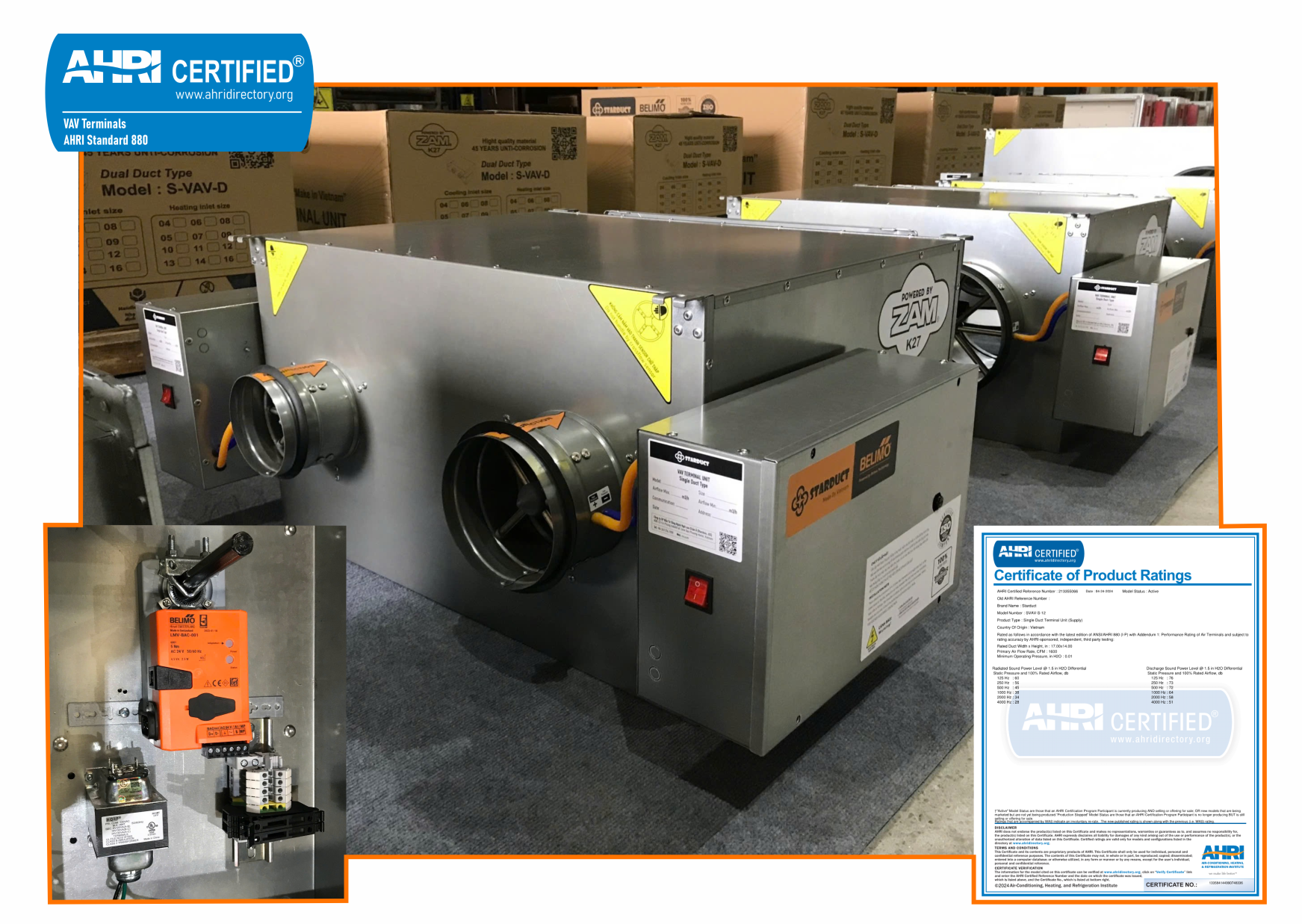
Control and Monitoring Strategies
Comparing Controllers – Belimo, Siemens, Honeywell, etc.
There are numerous VAV control equipment providers on the market, with notable names including Belimo, Siemens, Honeywell, Johnson Controls, and Schneider. Each company offers a product lineup that includes air damper actuators, sensors, and programmable controllers.
In terms of functionality, major brands deliver comparable features:
- Belimo offers its VAV Compact Controller line, which integrates a pressure sensor, controller, and actuator in a single unit. These support on/off control, 0–10V analog signals, or BACnet communication.
- Siemens provides the OpenAir series for VAV applications, with similar torque ratings and response times.
A comparison shows:
- Belimo LM series and Siemens GDE series are non-spring return actuators, directly mounted to VAV damper shafts.
- Both have approximately 45 in-lb (5 Nm) torque, powered by 24 VAC, and accept on/off, 3-point, or 0(2)–10 VDC control signals with position feedback.
- Full actuation time is around 90–95 seconds (some models are faster, ~30 seconds).
- Both brands feature position indicators and manual override levers, which are valuable for maintenance and emergencies.
Honeywell also offers VAV controllers like the Spyder and Jade series, which provide similar functionalities and are commonly integrated into Honeywell BMS systems.
Differentiators Between Brands
Key distinctions may include:
- Communication protocols supported: BACnet MSTP, Modbus RTU, LON, or proprietary options.
- Ease of programming: Siemens’ APOGEE vs. Honeywell’s WEBs platforms.
- Technical support and service availability.
- Belimo is known for highly reliable actuators and integrated models that simplify wiring.
- Siemens is strong in comprehensive building automation systems (BMS).
When choosing a controller, engineers should evaluate:
- System compatibility (whether using a single-vendor solution or integrating via BACnet)
- Add-on features (e.g., Belimo’s built-in delta-P sensor for easier retrofits, Honeywell’s Bluetooth-enabled mobile app for VAV calibration)
- Cost-effectiveness
Summary
All reputable brands offer controllers that meet standard VAV control requirements. Selection depends on the BMS ecosystem in the building and the experience of the system integrator.
DDC & BMS Architecture
Modern HVAC systems typically adopt a tree-like digital control architecture, consisting of:
- Field-level DDC controllers (for AHUs and VAVs)
- Supervisory or area controllers
- And a central BMS (Building Management System) server
In smaller projects, the intermediate level may be omitted, with VAV controllers communicating directly with the BMS.
- VAV controllers usually come pre-programmed (e.g., PID loops to modulate dampers, schedule reheat, maintain Q_min for ventilation).
- AHU controllers are more complex: managing supply air temperature, humidity (if applicable), damper positions (fresh/return/bypass air), and fan pressure via VFDs.
Communication protocols can include RS-485 (BACnet MSTP/Modbus RTU) or Ethernet (BACnet/IP) depending on system scale. The BMS software serves as the human-machine interface—handling dashboards, alarms, parameter tuning, and data logging.
A major benefit of this architecture is remote analysis: for instance, operators can review zone temperature trends or VAV damper positions over time to detect overloads or faulty sensors.
> As noted by integracontrols: “Both AHUs and VAV boxes are equipped with DDCs communicating over BAS. Overall monitoring and control are handled by the BMS, allowing operators to adjust setpoints and track system performance. This ensures coordination—for example, if a zone is too cold, BMS can command the AHU fan to slow down (via static pressure reset) or raise supply air temperature, rather than relying solely on local control. Advanced sequences can then be deployed system-wide.”
Basic vs. Advanced Control Logic
Basic Control
At its core:
- Each zone uses a local PID loop.
- Room temperature sensors send signals to the VAV controller, which modulates damper opening or reheat coils.
- In parallel, the AHU maintains:
- Fixed supply air temperature (e.g. 12.5°C) via chilled water valve modulation.
- Constant duct static pressure (e.g. 500 Pa) by adjusting fan speed.
This classic approach ensures comfort but may not optimize energy use under variable load conditions.
Advanced Control
Designed for greater efficiency without sacrificing comfort:
- Static Pressure Reset: Rather than keeping pressure high enough for the farthest VAV box, BMS monitors damper positions. If most are partially closed, it lowers fan pressure setpoint until 1–2 boxes are near full open (~90%). This aligns with Trim & Respond logic from ASHRAE Guideline 36.
- Supply Air Temperature Reset: If no zone requires strong cooling (e.g., VAVs <50%), BMS increases SAT, easing chiller load and reducing reheat demand. When cooling is needed (damper >90%), SAT drops again—saving more energy than maintaining 12°C year-round.
- Demand-Controlled Ventilation (DCV): Uses CO₂ sensors or usage schedules to modulate fresh air supply through AHU or VAV, ensuring indoor air quality with minimal outdoor air treatment.
- Occupancy-Based Setback: When rooms are unoccupied (via sensors or schedules), BMS raises HVAC setpoints slightly, reducing airflow to minimum levels. Comfort is restored upon re-occupancy—cutting off-hour consumption.
- Room Pressure Control: Especially in hospitals or cleanrooms, supply and return VAVs coordinate to maintain proper pressurization (+15 Pa for ORs, -15 Pa for isolation rooms).
These strategies rely on DDC logic and BMS supervision. Though programming is complex, ASHRAE Guideline 36 provides standardized sequences to enhance performance.
> Basic logic ensures functionality. Advanced logic fine-tunes operations for intelligence and efficiency—often saving an additional 10–20% in energy use.
Emerging Technologies – AI & IoT in VAV Systems
The rise of AI and IoT is redefining HVAC operations:
- Wireless IoT sensors (temperature, humidity, CO₂, occupancy) can integrate with VAV controllers.
- Data flows to the cloud, where AI algorithms analyze it to optimize HVAC behavior.
For example:
- AI learns room usage patterns—when it’s occupied, how many people, expected thermal load—and adjusts VAV schedules and dynamic setpoints accordingly.
- Predictive control anticipates needs (e.g., pre-cooling before occupancy), avoiding late reactions.
IoT also enables:
- Remote monitoring and control, even via virtual assistants or mobile apps.
- Predictive maintenance: AI flags anomalies like damper obstruction or motor efficiency loss by analyzing power consumption, airflow, and temperature data.
Future-ready systems include:
- Smart dampers with onboard microprocessors and sensors that act on AI-defined goals.
- Separation of control and logic layers: Unlike traditional thermostats tied to a single local sensor, an AI-IoT framework collects data from dozens of sensors per room and processes decisions in the cloud—delivering smarter control than conventional PID loops.
“IoT and AI are fundamentally reshaping how HVAC systems operate.”
