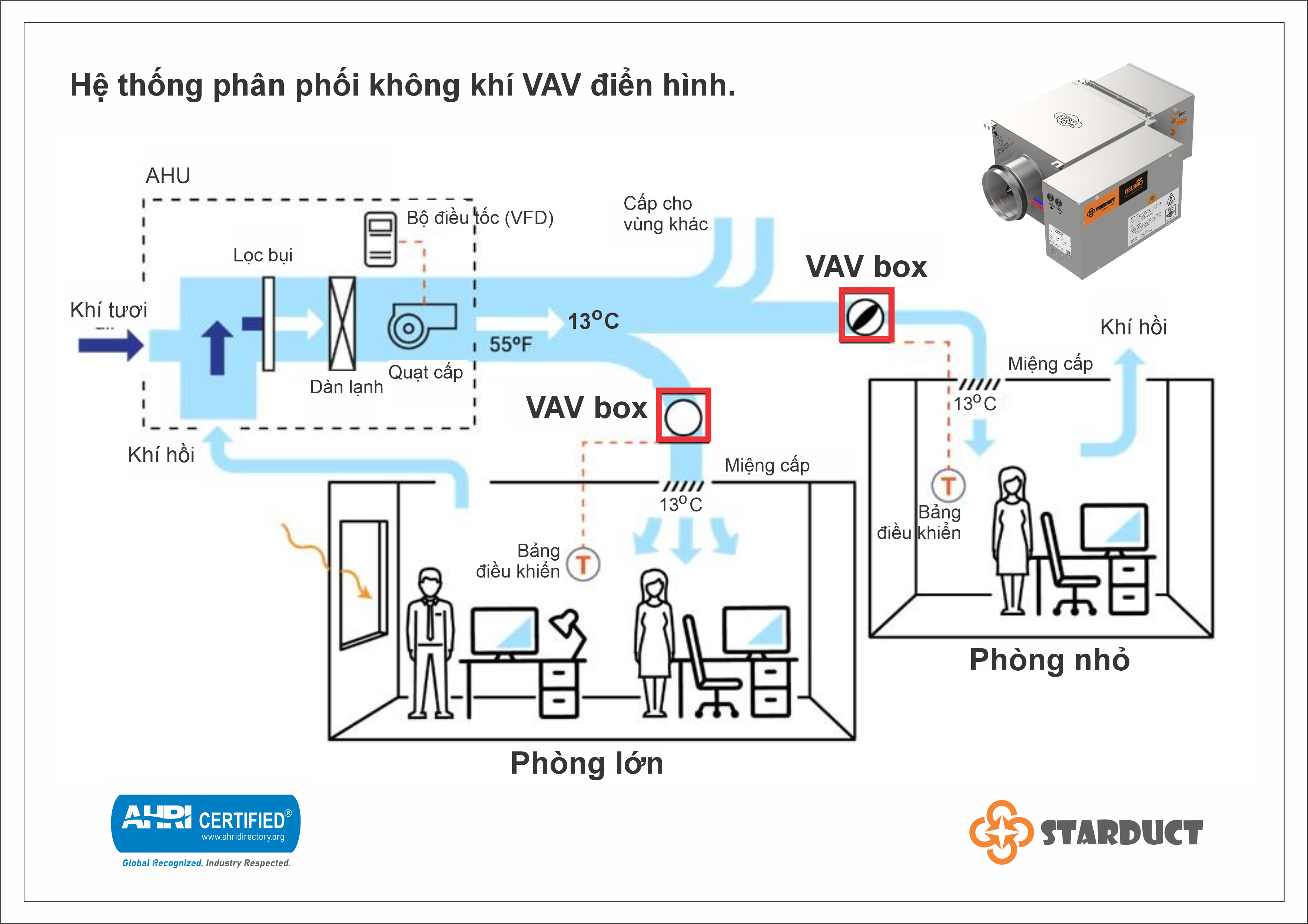
Efficient VAV System Design: Principles & Best Practices
Designing an effective Variable Air Volume (VAV) system requires a harmonious approach from the central plant to each zone. The core components include a central Air Handling Unit (AHU), zone-specific VAV terminal units, distribution ductwork, and a responsive control system.
VAV System Overview
In a typical setup, the central AHU supplies conditioned air at approximately 12°C through the main duct. Each VAV box—assigned per zone—modulates airflow via a damper to match the room’s thermal demand. Many boxes include airflow sensors and built-in controllers to ensure minimum ventilation is maintained, even during low load periods, avoiding complete shutoff of fresh air.
Types of VAV Terminal Units
- Single-Duct VAV with Reheat: Most common type, equipped with electric or hot water coils for reheating when necessary.
- Fan-Powered VAV: Incorporates a small fan to draw plenum air, aiding heating or supplementing airflow during peak loads.
- Dual-Duct VAV: Combines cold and hot air from separate ducts, mixing them to reach the desired zone temperature—used in systems with both hot and cold trunks.
Energy-Saving Control Strategies
Modern AHUs typically integrate Variable Frequency Drives (VFDs) for supply fans. These adjust fan speed based on system demand, significantly reducing energy use. A static pressure reset algorithm dynamically controls the fan to maintain pressure just sufficient for the “critical” (farthest open) VAV box. As more zones close their dampers, fan speed decreases to avoid excessive pressure—and wasted energy.
Additionally, supply-air temperature reset is used: when system-wide cooling demand drops, the AHU increases supply air temperature (e.g., from 12°C to 14–15°C), reducing chiller load and minimizing reheating needs at perimeter zones
Figure 1: Schematic of a typical HVAC system using VAV air distribution (AHU supplies cooled air into ductwork, which passes through VAV boxes to serve various zones). Each VAV box modulates airflow via a damper controlled by a zone-level DDC controller based on room temperature..
Zoning and VAV Layout
Effective zone design is key to a successful VAV system. The fundamental principle: each zone should have its own dedicated VAV box, allowing independent control based on that zone's specific thermal load. Zones are typically defined by areas with similar load characteristics and occupancy schedules—such as large rooms, clusters of west-facing offices, or densely occupied halls.
Engineers must calculate:
- Peak load per zone (e.g., cooling in summer, heating in winter)
- Maximum airflow (Q_max) for VAV box sizing
- Minimum airflow (Q_min) to meet ventilation needs (~30% of Q_max or based on fresh air standards)
VAV boxes should be positioned:
- Close to the conditioned area for accurate temperature sensing
- Away from quiet zones due to potential fan noise
- With short, low-resistance branch duct runs to reduce pressure loss and sound
Key Design Considerations
Aspect | Design Guidance |
---|---|
Duct Sizing | Use adequately sized ducts to limit pressure drop, while avoiding oversized ducts that consume space and inflate cost. Suggested air velocities: 5–7 m/s (main duct), 3–5 m/s (branches). |
VAV Box Placement | Locate near zones for responsive feedback; avoid long ducts that delay control. Allow access for maintenance (sensor replacement, damper servicing). |
System Configuration | Match zoning with space usage. For small offices, divide into smaller zones to minimize airflow when unoccupied. Open areas may need wide coverage with multiple sensors to avoid thermal imbalance. |
Future Flexibility | Design for adaptability—additional VAVs can be added if AHU capacity and controls permit. Leave room on ductwork for future expansion. |
Integration with AHU, Chillers, Heat Pumps & Controls
To optimize performance, a VAV system should be fully integrated across central cooling/heating and zone control levels:
- AHU & Chiller/Heat Pump: If using chilled water, it flows through AHU coils to cool air. When load decreases, BMS can reset chilled water temp or shut down extra chillers. In heating mode (via heat pump), coordinated control ensures warm water is supplied proactively (e.g., morning warm-up). Zone heating requests can signal the heat pump to start and deliver to AHU or VAV coils.
- A well-integrated system supports chilled/hot water reset based on average system demand—saving energy under part-load conditions.
DDC Controllers & BAS Communication
Each AHU and VAV terminal is equipped with a Direct Digital Controller (DDC) connected to the building network. Functions include:
- AHU DDC: Monitors supply air temp, duct pressure; controls VFD fans and cooling valves.
- VAV DDC: Monitors room temperature, airflow rate; modulates dampers and reheat valves (if any).
- All DDCs communicate through the Building Automation System (BAS) using standard protocols (BACnet, Modbus, LON).
The BMS supervisory software manages higher-level control such as:
- Scheduling
- Setpoint adjustments
- Alarm logging
- Data trend analysis
BAS enables advanced strategies:
- Static pressure reset (reduce fan speed if most VAVs are partially closed)
- Demand-Controlled Ventilation (DCV) using CO₂ sensors to modulate fresh air intake
This architecture allows real-time coordination between AHU and VAVs, maximizing comfort and energy savings.
In short: "Both the AHU and VAV boxes are equipped with DDCs and interconnected via the BAS. System monitoring and adjustments are typically performed centrally via the BMS interface, allowing remote management and performance optimization."
